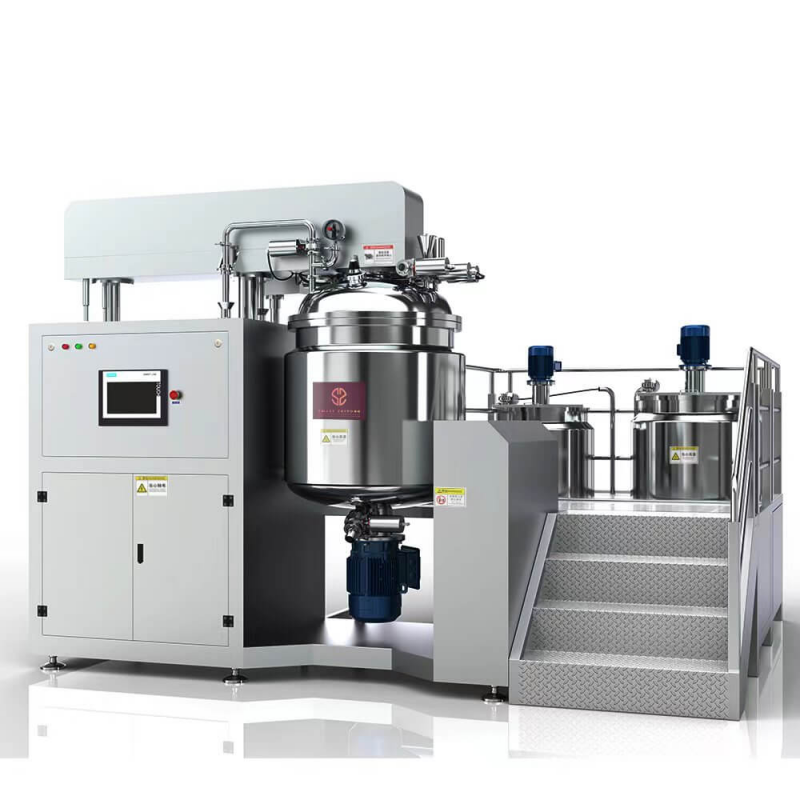
Vacuum Emulsifying Mixer It is a non-standard machine. Each Mixer is customized according to the specific requirements of the customer. When selecting a Vacuum Mixer Homogenizer, here is several key considerations must be taken into account to ensure that the Vacuum mixer meets the specific needs and requirements of the application. This guide outlines the primary factors to consider when purchasing for a Vacuum Emulsifying Mixer, covering technical specifications for Vacuum Emulsifying Mixer, material compatibility, scalability, ease of operation and maintenance, automation capabilities, safety features, and cost-effectiveness.
a. Capabilities for vacuum homogenizer cream mixer
1.Mixing Power and Speed: Determine the required mixing cream power and speed based on the viscosity and particle size of the materials being processed for a vacuum homogenizer cream mixer, Higher speeds and power force may be necessary. In order to reach customer's cream process requirements, cream mixer speed should be 0-65RPM, Homogenization speed should be 0-3600rpm.for special cream product need to 0-6000rpm, vacuum homogenizer cream mixer
Speed regulation requires the use of variable frequency drive step-less speed regulation
2..Shearing Action: Evaluate the shearing capabilities of the vacuum homogenizer cream mixer to ensure the effective breakdown of particles and emulsification of cream liquids. Homogenizer head speed should be 0-3600RPM Stepless speed regulation
3.Vacuum Level: Consider the desired vacuum level for the vacuum homogenizer cream mixer process. Higher vacuum levels can help remove more air bubbles and prevent oxidation. Generally, the vacuum level of the Vacuum Emulsifying Mixer should be -0.095Mpa to meet the requirements.
Model |
Effective capacity |
Homogenizer motor |
Stir motor |
Vacuum pupm |
Heating power(KW) |
|||||
KW |
r/min (option1) |
r/min (option2) |
KW |
r/min |
KW |
Limit vacuum |
Steam heating |
Electric heating |
||
FME-300 |
300 |
5.5 |
0-3300
|
0-6000 |
1.5 |
0-65 |
2.2 |
-0.085 |
32 |
12 |
FME-500 |
500 |
5.5 |
2.2 |
0-65 |
2.2 |
-0.085 |
45 |
16 |
||
FME-800 |
800 |
7.5 |
4 |
0-60 |
4 |
-0.08 |
54 |
25 |
||
FME-1000 |
1000 |
11 |
5.5 |
0-60 |
4 |
-0.08 |
54 |
25 |
||
FME-2000 |
2000 |
18.5 |
7.5 |
0-55 |
5.5 |
-0.08 |
63 |
25 |
||
FME-3000 |
3000 |
22 |
7.5 |
0-55 |
5.5 |
-0.08 |
72 |
25 |
1.Batch Size: Choose a vacuum emulsifying machine with a capacity that matches the required batch size. Ensure that emulsifying machine can handle both small-scale R&D batches and large-scale production runs. emulsifying machine single batch time is about 4-5 hours
2.Scalability: Look for emulsifying machine that can be easily scaled up or down to accommodate future growth or changes in production volumes.
3. Temperature Control and heating methods
Assess the temperature control capabilities of the emulsifying machine , including the ability to heat or cool the vacuum tanks during processing. This is crucial for maintaining the quality and integrity of heat-sensitive ingredients.
Model |
Effective capacity |
Minimum capacity(L) |
Max capacity (L) |
FME-300 |
300 |
100 |
360 |
FME-500 |
500 |
150 |
600 |
FME-800 |
800 |
250 |
1000 |
FME-1000 |
1000 |
300 |
1200 |
FME-2000 |
2000 |
600 |
2400 |
FME-3000 |
3000 |
1000 |
3600 |
- Vacuum Emulsifier Mixer has Electric heating used for mixer capacity below 500litres Generally, it has the following features:
a. High efficiency and energy saving
Fast heating speed: Vacuum Emulsifier Mixer’s Electric heating can quickly convert electrical energy into thermal energy, so that the internal temperature of the heated object rises rapidly, improving production efficiency.
b. High thermal efficiency: Since the heat of vacuum mixer is generated inside the heated object, the heat loss is reduced, so the thermal efficiency is high。
c. Easy to control accurate temperature control: The electric heating system of the Emulsifier Mixer can achieve precise temperature control and adjustment to meet the specified temperature of different processes.
d. High degree of automation: Vacuum Emulsifier Mixer combined with modern control technologies such as PLC (Programmable Logic Controller), Mixer can realize automatic control of the heating process and reduce manual intervention.
a. No pollution: No waste gas, waste residue or other pollutants are generated during the vacuum homogenizer cream mixer process, homogenizer mixer meets environmental protection requirements.
b.Keep clean: Heating in a vacuum environment can reduce the risk of oxidation and contamination, mixer keep the heated object clean
c. Strong processing capacity: vacuum homogenizer cream mixers of different models and specifications have different processing capacities to meet production needs of different scales.
When the Vacuum Mixer Homogenizer uses steam heating, it has the following salient features:
1. Uniform heating for vacuum homogenizer cream mixer
• Steam heating for vacuum homogenizer cream mixer can achieve uniform heating of materials in the
mixing container, avoiding changes in material properties caused by local overheating or uneven temperature. improving heating efficiency
b. High efficiency and energy saving, Steam is a clean energy source with high thermal efficiency. vacuum homogenizer cream mixer
does not produce harmful substances during the heating process and meets environmental protection requirements. same time, homogenizer cream mixer’s steam heating systems are usually equipped with heat recovery devices to recover and utilize waste heat to further improve energy efficiency.
c. Easy to control Steam heating systems for vacuum homogenizer mixer are usually equipped with temperature control devices, vacumm mixer can accurately control the heating temperature to meet the temperature requirements of different processes. By adjusting the flow and pressure of steam, vacuum cream mixer heating process can be easily controlled.
d: High safety for vacuum homogenizer mixer steam heating systems are relatively safe because steam is circulated in a closed system and is less likely to cause safety accidents for vacuum homogenizer cream mixer such as leakage and explosion. At the same time, the system is usually equipped with safety devices such as safety valves and pressure gauges to ensure the safety of the equipment during operation.
e. Wide range of applications: Steam heating is suitable for heating a variety of materials which are suitable for vacuum homogenizer cream mixer including materials with high viscosity, easy to agglomerate, and easy to oxidize. Steam heating in a vacuum environment can further reduce the risk of oxidation and contamination of materials and improve product quality.6. Strong flexibility
f. The steam heating system can be flexibly adjusted according to production needs.when a rapid temperature increase is required, the steam flow and pressure can be increased; when constant temperature is required, the steam supply can be adjusted to maintain a stable temperature.
Summary, when Vacuum Mixer Homogenizer uses steam heating, it has the characteristics of uniform heating, high efficiency and energy saving, easy control, high safety, wide application range and strong flexibility.
1.There are two structural designs of vacuum homogenizer on the market. Fixed vacuum emulsifying machine and hydraulic lifting vacuum homogenizer
Hydraulic lifting vacuum homogenizer has two types: single-cylinder and double-cylinder lifting vacuum homogenizer
a.Single-cylinder vacuum homogenizer is mainly used for machines less than 500L
b.Single-cylinder lifting vacuum homogenizer (vacuum homogenizer) has many advantages, homogenizer are mainly reflected in the following features
Single-cylinder lifting design: The single-cylinder lifting structure makes the vacuum homogenizer more compact as a whole, and is easy to install and use in small spaces.
c. Easy to operate: The single-cylinder lifting vacuum homogenizer controlled lifting vacuum homogenizer is relatively simple, and users can easily perform homogenizer lifting operations through the control panel, which improves work efficiency.
d. Efficient homogenization and emulsification
Efficient homogenization: Single cylinder lifting vacuum homogenizer is usually equipped with an efficient homogenization system,homogenizer can achieve efficient homogenization and emulsification of materials to ensure product quality
f,Wide applicability: Suitable for a variety of materials, including liquids, suspensions, powders, viscous fluids, etc., to meet the needs of different industries.
Single-cylinder hydraulic lifting vacuum homogenizer parameter
Model |
Effective capacity |
Emulsify |
Agitator |
Vacuum pupm |
Heating power | ||||
KW |
r/min |
KW |
r/min |
KW |
Limit vacuum |
Steam heating |
Electric heating |
||
FME-10 |
10 |
0.55 |
0-3600 |
0.37 |
0-85 |
0.37 |
-0.09 |
6 |
2 |
FME-20 |
20 |
0.75 |
0-3600 |
0.37 |
0-85 |
0.37 |
-0.09 |
9 |
3 |
FME-50 |
50 |
2.2 |
0-3600 |
0.75 |
0-80 |
0.75 |
-0.09 |
12 |
4 |
FME-100 |
100 |
4 |
0-3500 |
1.5 |
0-75 |
1.5 |
-0.09 |
24 |
9 |
FME-150 |
150 |
4 |
0-3500 |
1.5 |
0-75 |
1.5 |
-0.09 |
24 |
9 |
Double cylinder Vacuum Homogenizer is mainly used for machines larger than 500L
1. Free lifting and resetting: The double-cylinder hydraulic lifting system for the Vacuum Homogenizer can smoothly lift the pot cover and perform the inverted pot resetting operation, Homogenizer improves the flexibility and convenience of operation.
2. Strong stability: The vibration generated by the hydraulic system during the lifting process is minimized as Vacuum Homogenizer running, avoiding the shaking of the equipment during operation, and ensuring the stability and safety of the lifting process.
3. Strong carrying capacity: The hydraulic lifting system for Vacuum Homogenizer usually has a strong carrying capacity and can meet the lifting needs of heavier materials.
4. Easy maintenance: The maintenance of the hydraulic system for vacuum mixer is relatively simple. If a component has a problem, it is usually only necessary to replace the component to solve the problem.
5. Vacuum degassing and aseptic treatment
a.Vacuum degassing: The Vacuum Homogenizer works in a vacuum level, effectively removing bubbles in the material and improving the stability and appearance quality of the product.
b. Aseptic treatment: The environment of Vacuum Homogenizer also helps to meet aseptic requirements, especially suitable for industries such as food and medicine on hygiene conditions.
Double-cylinder hydraulic lifting system parameter
Model |
Effective capacity |
Homogenizer motor |
Stir motor |
Vacuum pupm |
Heating power |
||||
KW |
r/min |
KW |
r/min |
KW |
Limit vacuum |
Steam heating |
Electric heating |
||
FME-300 |
300 |
5.5 |
0-3300 |
1.5 |
0-65 |
2.2 |
-0.085 |
32 |
12 |
FME-500 |
500 |
5.5 |
0-3300 |
2.2 |
0-65 |
2.2 |
-0.085 |
45 |
16 |
FME-800 |
800 |
7.5 |
0-3300 |
4 |
0-60 |
4 |
-0.08 |
54 |
25 |
FME-1000 |
1000 |
11 |
0-3300 |
5.5 |
0-60 |
4 |
-0.08 |
54 |
25 |
FME-2000 |
2000 |
18.5 |
0-3300 |
7.5 |
0-55 |
5.5 |
-0.08 |
63 |
25 |
FME-3000 |
3000 |
22 |
0-3300 |
7.5 |
0-55 |
5.5 |
-0.08 |
72 |
25 |
Fixed-type vacuum emulsifying machines offer numerous advantages machine make them a highly sought-after choice for various industries, in cosmetics, pharmaceuticals, and food processing. Below are some of the key benefits of these machines,
a. Enhanced Production Efficiency for vacuum emulsifying machine
Fixed vacuum emulsifying machines significantly improve production efficiency compared to traditional methods or semi-automatic systems. machine automate the emulsification process, reducing manual intervention and labor costs while ensuring a consistent output.
b. Improved Product Quality
By operating under vacuum conditions, these machines eliminate the risk of contamination from airborne particles or moisture, ensuring a high-quality end product.. Additionally, precise temperature and mixing controls allow for tighter quality control, leading to superior product characteristics.
c. Versatility and Customization
Fixed vacuum emulsifying machines are highly versatile and can be customized to suit specific production requirements. They can handle a wide range of materials and formulations, from thick creams to thin lotions, making them suitable for a variety of applications across different industries. Manufacturers can adjust parameters such as mixing speed, temperature, and vacuum level to optimize the emulsification process for their unique product needs.
d. Energy Efficiency and Cost Savings
These machines are designed for energy efficiency, reducing power consumption during operation. This not only contributes to a greener production process but also leads to cost savings in the long run. Additionally, their durable construction and reliable performance ensure fewer breakdowns and maintenance requirements, further reducing operational costs.
Fixed vacuum emulsifying machine parameter
Model |
Effective capacity |
Homogenizer motor |
Stir motor |
Vacuum pupm |
Heating power |
||||
KW |
r/min |
KW |
r/min |
KW |
Limit vacuum |
Steam heating |
Electric heating |
||
FME-1000 |
1000 |
10 |
1400-3300 |
5.5 |
0-60 |
4 |
-0.08 |
54 |
29 |
FME-2000 |
2000 |
15 |
1400-3300 |
5.5 |
0-60 |
5.5 |
-0.08 |
63 |
38 |
FME-3000 |
3000 |
18.5 |
1400-3300 |
7.5 |
0-60 |
5.5 |
-0.08 |
72 |
43 |
FME-4000 |
4000 |
22 |
1400-3300 |
11 |
0-60 |
7.5 |
-0.08 |
81 |
50 |
FME-5000 |
5000 |
22 |
1400-3300 |
11 |
0-60 |
7.5 |
-0.08 |
90 |
63 |
a.Contact Materials: Ensure that the mixer homogenizer is made of high quality materials that are compatible with the materials being processed. including the mixing chamber, agitators, seals, and any other parts that come into contact with the mixture.
b.Corrosion Resistance: Choose materials that are resistant to corrosion and wear, especially if the mixture contains abrasive or corrosive ingredients.
b.Ease of Operation and Maintenance for Vacuum Homogenizer
Cleaning and Maintenance: Consider the design features that facilitate cleaning and maintenance, such as removable parts, smooth surfaces, and easy access to critical components.
Automation Capabilities for Vacuum Homogenizer
a.Programmable Controls: Look for machines with programmable controls that allow for the customization of mixing and homogenization parameters.
b.Sensors and Monitoring: Evaluate the availability of sensors and monitoring systems that provide real-time feedback on process parameters such as temperature, vacuum level, and mixing speed.
c.Integration with Other Systems: Consider the ability of the mixer homogenizer to integrate with other equipment and systems in the production line, such as filling and sealing machines.
d. Safety Features
1..Emergency Stop Buttons: Ensure that the machine is equipped with easily accessible emergency stop buttons to halt the process in case of an emergency.
2.Safety Guards and Enclosures: Look for machines with safety guards and enclosures that protect operators from moving parts and potential hazards.
3.Compliance with Safety Standards: Verify that the mixer homogenizer complies with relevant safety standards and regulations, such as CE, UL, or other international standards.
1.Initial Investment: Compare the initial cost of the mixer homogenizer with other options available in the market. Consider the balance between cost and performance.
2.Operating Costs: Evaluate the operating costs of the machine, including energy consumption, maintenance costs, and the cost of replacement parts.
Make summary
Selecting the right Vacuum Mixer Homogenizer requires careful consideration of multiple factors, including technical specifications, material compatibility, scalability, ease of operation and maintenance, automation capabilities, safety features, and cost-effectiveness. By taking these factors into account, manufacturers can choose a machine that meets their specific needs and helps them achieve their production goals.