In the fast-paced world of pharmaceutical and cosmetic industries, the efficiency and accuracy of manufacturing processes play a crucial role. One key aspect that demands utmost attention is ointment tube filling and sealing. To meet the increasing demand for precise and automated techniques, the industry has witnessed the emergence of advanced machines. In this blog, we delve into the advantages and functionalities of modern ointment tube filling and sealing machines, revolutionizing the production line.
1. Precise Filling Techniques
Manual ointment tube filling is a tedious and time-consuming task, leaving room for inconsistency and human error. However, with the advent of automated filling machines, manufacturers can now achieve precise product dosages with minimal wastage. These machines employ cutting-edge technology, providing a consistent and accurate filling process that meets stringent quality standards. From creams and gels to ointments and lotions, the machines allow for seamless adjustment, accommodating a wide range of viscosity levels, ensuring uniform product distribution.
2. Controlled and Reliable Sealing Process
Sealing the ointment tubes adequately is crucial to maintain product integrity and prolong shelf life. The manual sealing process is prone to variations, which can lead to improper sealing, leakage, and contamination. Ointment tube filling and sealing machines overcome these shortcomings with high-end sealing mechanisms. These machines apply the right amount of pressure, ensuring airtight seals consistently. Additionally, they can be tailored to suit different tube sizes and materials, offering manufacturers the flexibility to adapt to specific packaging requirements.
3. Enhanced Operational Efficiency
Opting for automated ointment tube filling and sealing machines significantly enhances operational efficiency for pharmaceutical and cosmetic industries. With automated processes, manufacturers can achieve higher production rates while minimizing production downtime. These machines are designed to handle large production volumes, streamlining the manufacturing process and reducing labor costs associated with manual labor. The machines are also equipped with user-friendly touch interfaces and programmable controls, allowing easy operation and quick product changeovers, further maximizing efficiency.
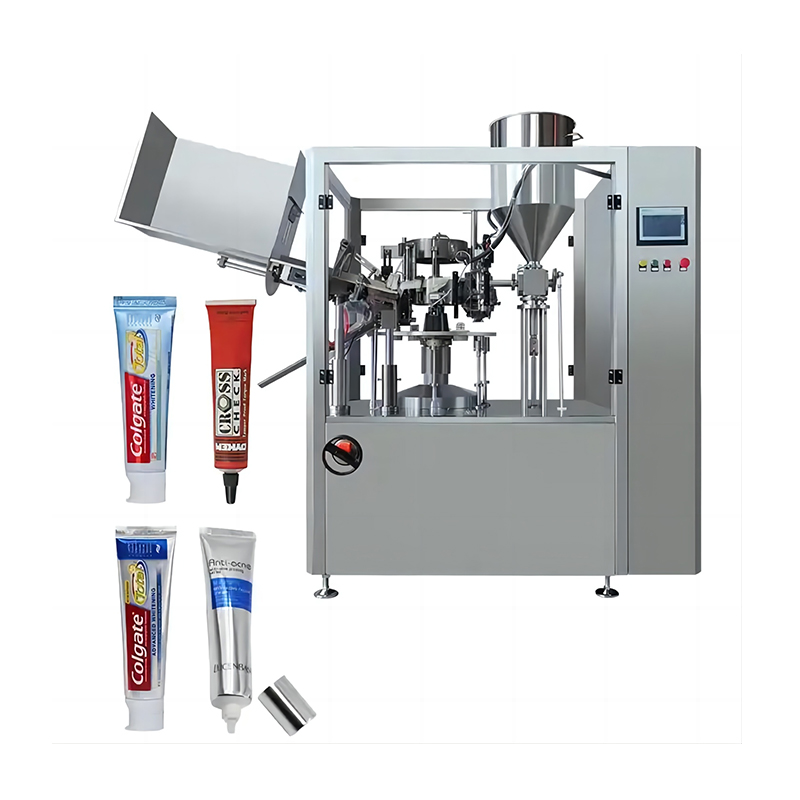
4. Improved Safety Standards
Ensuring the safety and wellbeing of both end-users and production personnel is of paramount importance in the pharmaceutical and cosmetic industries. Modern ointment tube filling and sealing machines prioritize safety features during the manufacturing process. With advanced sensor technologies, these machines automatically detect any faults or irregularities, preventing issues like tube blockages, incorrect pressure variations, or faulty seals. Manufacturers can be assured that the final product meets the highest safety standards, minimizing the risks of product recalls or customer dissatisfaction.
The integration of ointment tube filling and sealing machines within pharmaceutical and cosmetic industries revolutionizes manufacturing processes, guaranteeing precision, reliability, efficiency, and safety, while also ensuring customer satisfaction.
In today's competitive business landscape, in advanced ointment tube filling and sealing machines is not only a strategic move but also a necessity. By embracing automation, manufacturers can achieve higher production rates, minimize wastage, and maintain quality standards, ultimately gaining a competitive edge in the market.
If you have concerns please contact
Post time: Nov-14-2023