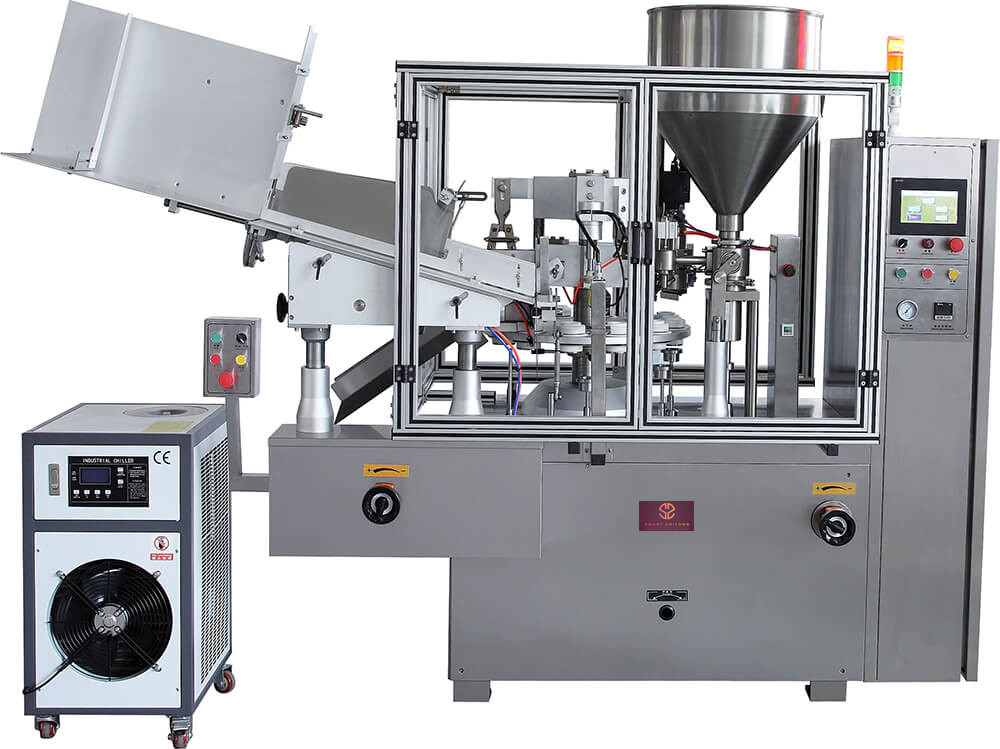
The whole Cosmetic Tube Filling and Sealing Machine is made of high-quality stainless steel for all contacting materials and certain related parts. The parts that need to be cleaned are all equipped with quick-change devices, which are easy to disassemble and wash. When some materials need to be heated and kept warm, a heating constant temperature device can be installed outside the barrel. Any material that uses plastic pipes and composite pipes as packaging materials can be confidently selected by this machine. It is the best product selected by the cosmetics industry, pharmaceutical industry, adhesive industry, shoe polish industry and other related industries
The compound tube filling and sealing machine can smoothly and accurately inject various pasty, creamy, viscous fluids and other materials into the hose, and then complete the heating of the hot air in the tube, sealing, batch number, production date, etc. The filling and sealing machine is widely used in the filling and sealing of large-diameter plastic pipes and composite pipes in industries such as medicine, food, cosmetics, and daily chemical products. It is an ideal, practical and economical filling equipment.
Cosmetic Tube Filling and Sealing Machine Features:
◆The high-grade liquid crystal display programming controller and the operation video screen combined with buttons can comprehensively grasp the operation status of the equipment such as stepless speed regulation, parameter equipment, output counting statistics, air pressure indication, fault display, etc., making the operation simple and humanized.
◆Manually or automatically put the materials to be filled into the feeding bin, and then the filling and sealing can be completed automatically.
◆The high-precision marking system reduces the range of color difference between the tube body and the color mark.
◆External adjustment part, position digital display, fast and accurate adjustment (suitable for multi-specification and multi-variety production).
Cosmetic Tube Filling and Sealing Machine Attention to details during maintenance
1. All lubricating parts should be filled with sufficient lubricant to prevent mechanical wear.
2. During the operation, the operator should operate in a standardized manner, and it is not allowed to touch the various components of the machine tool while it is running, so as to avoid personal injury accidents. If any abnormal sound is found, it should be shut down in time to check until the cause is found out, and the machine can be turned on again after the fault is eliminated.
3. The lubricator must be filled with oil (including the feeding unit) before each start-up of production
4. Release the accumulated water of the pressure reducing valve (including the feeding unit) after shutting down after each production
5. Clean the inside and outside of the filling machine, and it is strictly forbidden to wash with hot water higher than 45°C, so as not to damage the sealing ring.
6. After each production, clean the machine and turn off the main power switch or unplug the power plug.
7. Regularly check the sensitivity of the sensor
8. Tighten the connecting parts.
9. Check the electric control circuit and the connection of each sensor and tighten them.
10. Check and test whether the motor, heating system, PLC, and frequency converter are normal, and perform a cleaning test to see if each coefficient parameter is normal.
11. Check whether the pneumatic and transmission mechanism are in good condition, and make adjustments and add lubricating oil.
12. Equipment maintenance items are handled by the operator and maintenance records are made.
Smart Zhitong is a comprehensive and diversified packaging machinery and equipment enterprise integrating design, production, sales, installation, and service. It is committed to providing you with sincere and complete pre sales and after-sales services, benefiting the field of chemical equipment
Website:https://www.cosmeticagitator.com/tubes-filling-machine/
Post time: Mar-21-2023