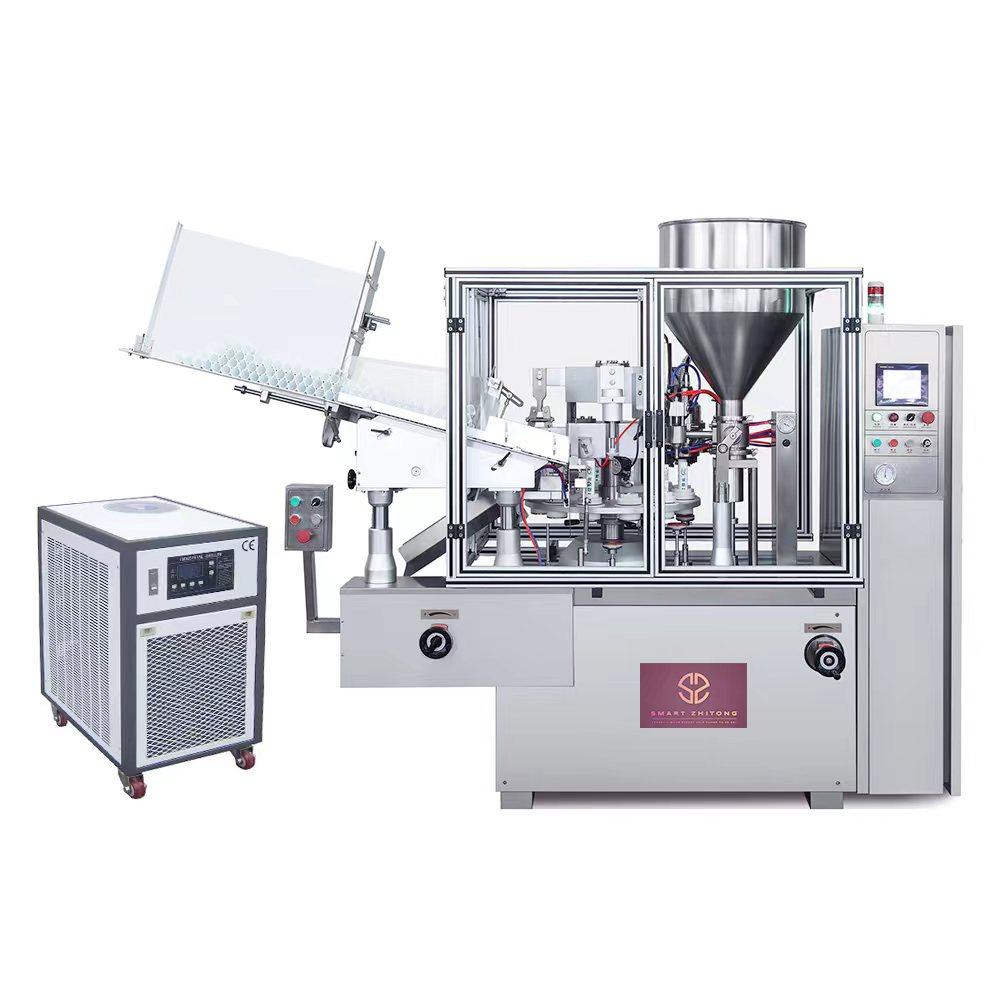
Eighteen debugging methods
Item 1 Function and adjustment of photoelectric switch
The photoelectric switch is installed on the filling and metering lifting seat as a given signal for pressing the tube, filling, heating, and tail pressing. The photoelectric switch detects the pressing tube station, so when the The indicator light of the photoelectric switch should be on (if it is not on, adjust the detection position of the photoelectric switch, if the position is aligned with the indicator light and it is not on, you can adjust the detection distance of the photoelectric switch. The distance becomes longer, and vice versa), when the photoelectric switch of Automatic Filling and Sealing Machine detects the tube, the tube pressing, filling, heating, and tail pressing will work accordingly.
Item 2 Adjustment of the color mark sensor
The color mark sensor of Automatic Tube Filler and Sealer is installed at the automatic color mark station. When the main turntable divider stops running, the ejector rod driven by the color mark cam and the hose in the cup holder rise to the highest position, and the retractable centering rod is lifted at the same time. , the proximity switch light of Automatic Tube Sealing Machine installed on the centering rod is on, and the stepping motor for measuring the color mark rotates. If the color mark sensor receives a signal at this time, the stepping motor rotates in place at the set eccentric angle, and the motor stops running. To adjust the color mark sensor, when the cam is raised (there is a tube in the cup holder, and the position of the color mark on the tube is just in the middle of the color mark sensor probe, with a distance of about 11mm), manually rotate the cup holder to make the position of the color mark Deviate from the color mark probe, press the switch on the color mark sensor at the same time, the indicator light will flash, then rotate the cup holder so that the color mark position is facing the color mark probe, press the button on the color mark sensor again, and the light should be on at this time; back and forth Turn the cup holder to rotate the hose, and if the indicator light is flashing, it means that the color mark sensor has been adjusted, otherwise, continue to adjust until it is adjusted.
Item 3 Adjustment of the proximity switch of Automatic Tube Filling Sealing Machine
The proximity switch has two installation positions, one is installed at the end of the input shaft of the main turntable divider, and the other is installed at the color standard station. The proximity switch will only use the signal when the metal object is within a certain distance (within 4mm). output (indicator lights up).
Item 4: Adjustment of tube bins and upper tube handrails of Automatic Tube Filling Sealing Machine
First check that the pipe bucket is installed correctly. The correct installation has a backward inclination that is the angle with the horizontal plane,
When adjusting, please loosen the fastening screw of the pipe bucket first, and rotate it backward along the rotating shaft at a certain angle (about 3-5 degrees). Note that the height and inclination angle of the bottom plate of the pipe bucket guide rail after adjustment should be consistent with the upper pipe handrail. For hoses of different specifications, corresponding adjustments should be made, loosen the fastening screws, and move the guide rail baffle up and down, left and right, so that the hose can flow down the guide rail smoothly with a minimum gap.
To adjust the handrail of the upper tube, first place the prepared hose on the bottom plate of the tube chamber, let the head of the hose naturally roll down to the handrail of the upper tube along the track baffle, then hold the handrail and press the hose to make it move forward Rotate until it is perpendicular to the turntable. At this time, adjust the height of the support base of the tube warehouse so that the distance between the tube cover plane of the hose and the upper plane of the tube cup is 5-10 mm, and adjust the handrail so that the centerline of the hose coincides with the centerline of the tube cup. Note: The height adjustment of the support base of the tube warehouse is completed by rotating the support screw. After the adjustment, the fastening screws on the support base should be locked. Then adjust the bottom plate of the tube bin to be on the same plane as the upper plane of the upper tube armrest.
Eighteen debugging methods including tube filling and sealing machine amplifier, color mark sensor, etc.
Item 3 Adjustment of the proximity switch for Automatic Tube Sealing Machine
The proximity switch has two installation positions, one is installed at the end of the input shaft of the main turntable divider, and the other is installed at the color standard station. The proximity switch will only use the signal when the metal object is within a certain distance (within 4mm). output (indicator lights up).
Item 4: Adjustment of tube bins and upper tube handrails for automatic tube filling machine
First check that the pipe bucket is installed correctly. The correct installation has a backward inclination that is the angle with the horizontal plane,
When adjusting, please loosen the fastening screw of the pipe bucket first, and rotate it backward along the rotating shaft at a certain angle (about 3-5 degrees). Note that the height and inclination angle of the bottom plate of the pipe bucket guide rail after adjustment should be consistent with the upper pipe handrail. For hoses of different specifications, corresponding adjustments should be made, loosen the fastening screws, and move the guide rail baffle up and down, left and right, so that the hose can flow down the guide rail smoothly with a minimum gap.
To adjust the handrail of the upper tube, first place the prepared hose on the bottom plate of the tube chamber, let the head of the hose naturally roll down to the handrail of the upper tube along the track baffle, then hold the handrail and press the hose to make it move forward Rotate until it is perpendicular to the turntable. At this time, adjust the height of the support base of the tube warehouse so that the distance between the tube cover plane of the hose and the upper plane of the tube cup is 5-10 mm, and adjust the handrail so that the centerline of the hose coincides with the centerline of the tube cup. Note: The height adjustment of the support base of the tube warehouse is completed by rotating the support screw. After the adjustment, the fastening screws on the support base should be locked. Then adjust the bottom plate of the tube bin to be on the same plane as the upper plane of the upper tube armrest.
Eighteen debugging methods including tube filling and sealing machine amplifier, color mark sensor, etc.
Item 5 Adjustment of pressure tube cylinder for automatic tube filling machine
Loosen the adjustment screw of the pressure tube cylinder, first make the axis and the center line of the cone head coincide with the center of the hose at the upper tube station, and then adjust the height to the end position of the pressure tube cylinder when the piston shaft is stretched out. It is advisable when the head and the end of the pipe just touch.
Item 6 Adjustment of drive top tube armrest cam linkage for Automatic Tube Filler and Sealer
According to the adjusted height of the turntable and the tube bin, adjust the cam link of the upper tube handrail accordingly, so that the upper tube handrail is in the same plane with the bottom rail plate of the tube bin at the starting position, and the end position is perpendicular to the turntable.
Item 7: According to the change of the diameter and length of the hose, the coordination between the upper tube, the release tube, and the pressure tube is adjusted in terms of time. Before using a new machine or after switching hoses of different specifications, these three actions must be checked. If they are not coordinated, please correct them in the parameter column。
Item 8 Adjustment of tube storage arrangement, for Automatic Tube Filling Sealing Machine
The machine has been adjusted according to the hose provided by you when it leaves the factory (generally), the adjustment method given in this article is for adjustments due to various reasons (such as transportation, conversion of specifications, or no hose provided to the manufacturer before leaving the factory or other reasons) for the operator's on-site reference.
Item 9 Adjustment of color mark sensor and pressure cone
Adjust the stop position of the color mark of the hose (for the specific adjustment method, please refer to the manufacturer's instructions of the SICK or BANNER color mark sensor bound in the manual).
On the color code station, the function of the hose pressure cone is to give some pressure to the hose to control the correct positioning and correct movement of the hose in the tube cup. There is a minimum pressure between them that will not slip when rotating. The cone The center of the head should coincide with the center of the hose, and the shape of the cone should be determined according to the diameter of the hose.
Item 10 Adjustment of end-sealing and typing code manipulator for Automatic Tube Sealing Machine
Insert a hose into the tube cup, turn it to the embossing and sealing station, and turn the hand to make the imprinting jaws in a closed state. At this time, observe that the plane of the tail of the hose should be at the same level as the plane of the crimping board. on flat surface. If you want to change the width of the tail, please loosen the set screws of the jaws, and then adjust the height of the jaws accordingly. To adjust the gap between the inner and outer jaws, turn the hand to make the inner and outer jaws in a closed state without a hose. At this time, observe that there is no gap between the inner and outer jaws (the inner and outer jaws The jaws should be parallel to each other in the direction perpendicular to the turntable, and the bottom surfaces of the two jaws should be on the same plane).
Item 11 Shearing (trimming the hot-melt and pressing part of the tail of the hose) manipulator
If the tail of the hose is incompletely cut or roughened during the cutting process, first check whether the two blades are sharp (if the blade is blunt or unsharp after being used for too long or the material of the hose is too hard, a professional inspection should be carried out in time). Grinding or replacing a new knife to solve), at the same time observe whether there is a gap in the contact edge when the inner and outer blades are closed (if there is a gap, you can adjust the pressure of the two compression springs or take a copper sheet of corresponding thickness as a cushion according to the size of the gap. On the blade at the end with a larger gap, so that the inside and outside edges are parallel).
12 test runs
After the above preparations are completed, please conduct a test run on the main engine. Before running, first close the safety door, set the test run speed on the touch screen (the lowest speed that can make the machine start and run), and first use the jog switch (continuously press-release- Press - release,) several times to observe that there is no abnormality in the equipment, then press the main engine start switch, run the main engine for about 3 minutes, and check the working conditions of each part at the same time. After confirming that everything is normal, set the main engine speed to the speed required by the production process.
Connect the compressed air source, adjust the pressure regulating valve, so that the number displayed on the air pressure gauge is the set air pressure (the air pressure value is generally a fixed value of 0.5Mpa-0.6Mpa)。
Touch the heating switch, the hot air generator starts to work, and the temperature controller displays the set temperature. After 3-5 minutes, the outlet temperature of the hot air generator reaches the set working temperature (depending on the material, material, wall thickness, and temperature of the hose per unit time). Factors such as the number of potting times and the ambient temperature determine the heating temperature of the hot air generator (the plastic composite pipe is generally 300-450°C, and the aluminum-plastic composite pipe is generally 350-500°C).
Item 13 Replacement of tube cup core
It is very simple to replace the inner core of the tube seat according to different hose diameters and hose shapes.
item 14 filling Nozzles for automatic tube filling machine
Different sizes of hoses need to be equipped with injection nozzles with different apertures. The aperture of the injection nozzle is determined by comprehensive factors such as the diameter of the hose, the specific gravity and viscosity of the injected liquid, the filling volume, and the production speed.
Item 15 Selection and adjustment of dosage pumps
The filling dose of the material is consistent with the hose, and the diameter of the piston is selected according to the dose.
Piston diameter 23mm Filling volume 2-35mL
Piston diameter 30mm Filling volume 5-60mL
Piston diameter 40mm Filling volume 10-120Ml
Piston diameter 60mm Filling volume 20-250Ml
Piston diameter 80mm Filling volume 50-400Ml
A larger filling range can be obtained by replacing the piston (changing the piston diameter) and adjusting the filling stroke.
Item 16 Chain Tension Adjustment
Loosen the fixing bolts and adjust the position of the chain tensioner to make the chain tension moderate.
Item 17 Adjustment of air pressure
Adjust the pressure regulating valve to make the normal working air circuit pressure reach a constant value (the total air pressure is generally 0.60Mpa, and the upper pipe air pressure is generally 0.50-0.60Mpa)
Item 18 Paste tail blowing off compressed air regulation
The function is: after each hose is filled, the adhesion (paste tail) on the injection nozzle will be blown off. The method is: according to the characteristics of the ointment, turn the adjustment knob by hand to the corresponding air volume, and then tighten the fastening nut after adjustment.
Smart Zhitong has many years of experience in the development, design Automatic Tube Filler and Sealer automatic tube filling machine offer customize service
If you have concerns please contact
@carlos
Wechat WhatsApp +86 158 00 211 936
For more type of aluminum tube filling machine please visit please visit https://www.cosmeticagitator.com/tubes-filling-machine/
Post time: Dec-12-2022