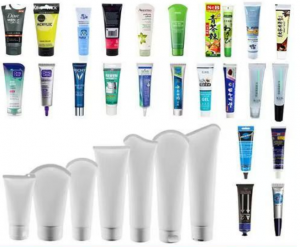
Tube filling machine is a very important packaging machine in today's industrial age. It is widely used in cosmetics, food, pharmaceutical and other industries. Sealing process is extremely important. If the sealing tail effect is not good, it will cause great harm to the safety and quality of the product, thus bringing great danger to consumers. To ensure the sealing effect of the filling tail seal, the following aspects can be considered and operated:
1. The core heating parts of the tube filling machine are selected. Most customers in the market use Swiss Leister internal heating air guns, and give priority to models with independent programmable, with an accuracy of ±0.1 Celsius.
2. The hot air gun sealing pipe fittings are made of high-quality and high-conductivity copper parts, and are processed by high-precision CNC machine tools. Guarantee the processing accuracy.
3. Use an independent refrigerator to provide coolant to the plastic tube filling and sealing machine to ensure constant temperature. The coolant cools the hot air gun at a constant pressure and flow rate to achieve the best cooling effect.
Tube filling machine Technical Parameters
Model no | Nf-40 | NF-60 | NF-80 | NF-120 | NF-150 | LFC4002 |
Tube material | Plastic aluminum tubes .composite ABL laminate tubes | |||||
Station no | 9 | 9 | 12 | 36 | 42 | 118 |
Tube diameter | φ13-φ50 mm | |||||
Tube length(mm) | 50-210 adjustable | |||||
viscous products | Viscosity less than 100000cpcream gel ointment toothpaste paste food sauce and pharmaceutical, daily chemical, fine chemical | |||||
capacity(mm) | 5-210ml adjustable | |||||
Filling volume(optional) | A:6-60ml, B:10-120ml, C:25-250ml, D:50-500ml (Customer made available) | |||||
Filling accuracy | ≤±1% | ≤±0.5% | ||||
tubes per minute | 40 | 60 | 80 | 120 | 150 | 300 |
Hopper Volume: | 30litre | 40litre | 45litre | 50 litre | 70 litre | |
air supply | 0.55-0.65Mpa 30 m3/min | 40m3/min | 550m3/min | |||
motor power | 2Kw(380V/220V 50Hz) | 3kw | 5kw | 10KW | ||
heating power | 3Kw | 6kw | 12KW | |||
size(mm) | 1200×800×1200mm | 2620×1020×1980 | 2720×1020×1980 | 3020×110×1980 | 3220×140×2200 | |
weight (kg) | 600 | 1000 | 1300 | 1800 | 4000 |
一、1. Process adjustment to ensure sealing effect
Temperature is the first factor that affects the firmness of the tube filling machines' sealing. Plastic tube filling and sealing machine adopts internal heating and sealing. Obviously, too low temperature will cause the tube tails material to not fully melt, and the tube tail can not fuse during machine sealing processing, but too high temperature may cause the sealing plastic material to melt excessively, resulting in deformation, thinning, etc., causing sealing result leakage.
Adjust the temperature of the internal heater step by step according to the type and thickness of the sealing material. Generally, you can start from the lowest temperature range recommended by the tube supplier, and adjust the range by 5~10℃ each time, then conduct a sealing test, observe the sealing effect, test the pressure resistance through a pressure gauge, and record it until the best temperature is found.
Investigation2.Bonding pressure parameter setup
The appropriate bonding pressure can make the materials at the sealing point fit tightly and ensure the sealing effect. When the pressure is insufficient, there may be a gap in the tube tail material and it cannot form a strong bond; excessive pressure may damage the sealing material or cause uneven deformation of the sealing.
Solution: Check whether the compressed air pressure of the filling machine is within the specified range, check and adjust the device, adjust the pressure according to the characteristics of the sealing material and the specifications of the tube thickness machine tube size in diameter in, increase or decrease the pressure in a small range (such as 0.1~0.2MPa) during adjustment, and then conduct a sealing test to check the firmness of the sealing. At the same time, check the batch tube size consistency。
Investigation3,bonding time setup :
If the bonding sealing time is too short, the tube tails material may not be fully fused before the sealing process is completed; if the sealing time is too long, it may have a bad effect on the sealing material.
Solution: Adjust the sealing time according to the performance of the equipment and the requirements of the sealing material. If it is the first time to debug, you can start from the reference time provided by the material supplier, and increase or decrease the time appropriately according to the sealing effect, with each adjustment range of about 0.5~1 second, until the sealing is firm and looks good.
二、Tube filling machines maintenance and inspection
1. Inspection and replacement of tail sealing mold:
Investigation, hot air sealing part may be worn after long-term use, resulting in irregular tail sealing shape or uneven tail sealing pressure.
Solution: Regularly check the wear of hot air sealing part. If scratches, dents or wear on the part surface exceed a certain limit, the mold should be replaced in time.
2. Inspection and replacement of heating element:
Hot air gun component failure or heating program may cause uneven heating of the tail sealing part, so that the tail sealing material cannot be fully melted.
Solution: Check whether the hot air element is damaged, short-circuited or in poor contact. Use detection tools (such as multimeter) to detect whether the resistance value of the heating element is within the normal range. If the element is damaged, please replace it with a heating element of the same model quickly.
3. Equipment cleaning and lubrication:
When Tube Filling Machines are running, due to long-term operation, some materials may remain on the tail sealing parts, which need to be cleaned manually immediately. These residues will affect the quality of the tail sealing.
Solution: According to the instruction manual of Tube Filling Machine, regularly lubricate the relevant transmission parts and use appropriate lubricants. At the same time, regularly clean the residues at the sealing end to ensure the cleanliness of the sealing end.
三、Choose the appropriate plastic tube material,
1. Tube material selection:
The quality and characteristics of different plastic materials have a significant impact on the firmness of sealing tails. If the sealing material and formula are unreasonable, the purity is insufficient or there are impurities, the sealing will be unstable.
Solution: Select reliable quality sealing materials to ensure that they meet production requirements
2. Tube size specification selection:
The material, size, surface smoothness and other factors of the tube may also affect the sealing effect. For example, the rough surface of the tube may cause the sealing material to not adhere evenly, thus affecting the sealing performance.
Solution: Select suitable tubes to ensure that their dimensional accuracy and surface quality meet the requirements. For tubes with rough surfaces, pretreatment such as grinding and cleaning can be considered to improve the sealing effect. When selecting materials, it is necessary to detect the characteristics of the materials and conduct multiple tests.
Environmental control temperature and humidity, monitor and condition them
Changes in ambient temperature and humidity may affect the physical properties of the sealing material and produce different results in sealing tails. For example, if the tube is in a high humidity environment, the sealing material may absorb a lot of moisture, which will affect its melting and fusion effect when sealing the tail at high temperature; too low a temperature may make the material brittle, which is not conducive to sealing.
Post time: Nov-07-2024